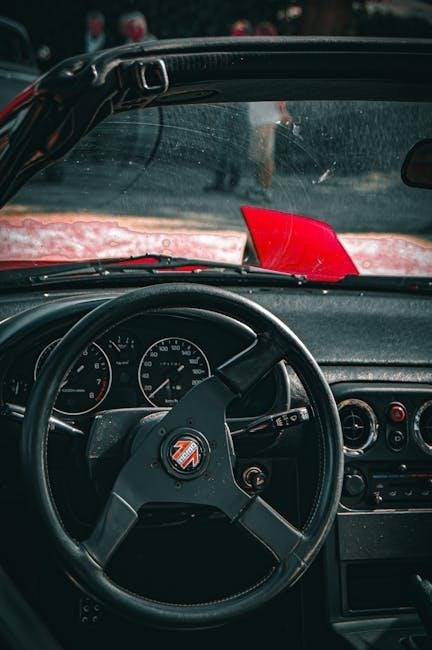
The Allen-Bradley PowerFlex 525 drive is a versatile and efficient AC drive designed for industrial motor control, offering advanced features for optimal performance and energy efficiency.
1.1 Overview of the PowerFlex 525 Series
The PowerFlex 525 series is a line of adjustable frequency AC drives designed for industrial motor control, offering compact, versatile, and user-friendly solutions. These drives are ideal for applications requiring precise speed and torque control, such as pumps, fans, and conveyors. With advanced features like variable frequency control and remote monitoring, the PowerFlex 525 series ensures energy efficiency and seamless integration with industrial automation systems. Its robust design and reliability make it a preferred choice for various industries, including manufacturing, oil and gas, and water treatment. The series is backed by comprehensive documentation and technical support.
1.2 Key Features and Benefits
The PowerFlex 525 drive offers a compact design, ease of use, and advanced control capabilities, making it ideal for industrial applications. It supports multiple control modes, including V/Hz and sensorless vector control, ensuring precise motor operation. The drive features energy-efficient performance, reducing operational costs, and integrates seamlessly with PLC and SCADA systems for enhanced automation. Its user-friendly interface and remote monitoring capabilities simplify operation and maintenance. With robust safety features and compliance with industry standards, the PowerFlex 525 ensures reliable and secure performance. These features make it a top choice for industries requiring versatile and efficient motor control solutions.
1.3 Importance of the Manual for Optimal Usage
The PowerFlex 525 drive manual is essential for safe, efficient, and effective operation. It provides detailed instructions for installation, configuration, and troubleshooting, ensuring users avoid common pitfalls. The manual outlines parameter settings, control modes, and safety protocols, helping users maximize performance. It also covers compliance with industry standards and maintenance procedures, ensuring longevity and reliability. Without the manual, users may miss critical configurations or overlook safety measures, leading to suboptimal operation or potential damage. Referencing the manual is crucial for both novice and experienced users to fully harness the drive’s capabilities and maintain operational excellence.
Installation and Setup of the PowerFlex 525 Drive
Proper installation ensures safe and efficient operation. Follow guidelines for unpacking, physical mounting, and electrical connections. Initial power-up and configuration must align with manual instructions.
2.1 Unpacking and Physical Installation
Carefully unpack the PowerFlex 525 drive, ensuring all components are included and undamaged. Handle the drive with caution to avoid physical stress. Mount the drive in a well-ventilated, dry area, ensuring proper grounding to prevent electrical interference. Follow the installation guidelines in the manual to secure the drive firmly. Verify the nameplate ratings match your application requirements before proceeding. Proper physical installation is critical for safe and reliable operation. Always adhere to safety standards and manufacturer recommendations during the setup process to avoid potential hazards and ensure optimal performance.
2.2 Electrical Connections and Wiring Requirements
Proper electrical connections are essential for the PowerFlex 525 drive’s operation. Ensure the jumper between terminals 1 and 11 is in place, as its removal can prevent the drive from running. Connect the three-phase power supply to terminals L1, L2, and L3, and ensure the motor is wired to the drive’s output terminals. Ground the drive to prevent electrical noise and hazards. For control connections, wire external signals like start/stop and speed references according to the manual. Use shielded cables to reduce interference and follow the manual’s wiring diagram for specific instructions. Verify all connections before powering up to ensure reliable operation.
2.3 Initial Power-Up and Basic Configuration
After completing the electrical connections, power up the drive and check for any fault codes. Use the keypad to navigate through the menu and ensure all settings are correct. Configure basic parameters such as motor nameplate data, control mode, and speed references. Verify communication settings if integrating with a PLC or other systems. Refer to the manual for default settings and customization options. Ensure all safety features are enabled and test the drive in manual mode before integrating it into your larger system. Proper configuration ensures smooth operation and prevents potential issues.
Programming and Parameter Settings
The PowerFlex 525 requires precise parameter configuration to optimize performance, including motor tuning, control mode selection, and customizing settings for specific applications.
3.1 Understanding the Parameter Structure
The PowerFlex 525 drive features a comprehensive parameter structure that organizes settings into logical groups, such as motor control, I/O configuration, and advanced features. These parameters are accessed through software tools or the drive’s interface, enabling users to customize operation for specific applications. Proper understanding of the parameter structure is essential for achieving optimal performance, as incorrect settings can lead to suboptimal operation or even faults. The user manual provides detailed explanations and guidelines for navigating and adjusting these parameters effectively. Regular updates to the manual ensure compatibility with the latest firmware and hardware configurations.
3.2 Configuring Motor Parameters for Optimal Performance
Configuring motor parameters is critical for ensuring the PowerFlex 525 drive operates efficiently and safely. Key settings include motor nameplate data, such as rated voltage, current, and frequency, which must match the connected motor. Parameters like motor inertia and load type also impact performance. Accurate configuration prevents issues like motor overload or overheating. The drive allows customization of torque, speed, and acceleration/deceleration rates to suit specific applications. Advanced settings, such as slip compensation and vector control, further optimize motor performance. Always refer to the user manual for detailed guidance on motor parameter configuration. Incorrect settings can lead to suboptimal operation or faults.
3.3 Setting Up Control Modes (V/Hz, Sensorless Vector, etc.)
The PowerFlex 525 drive supports multiple control modes to suit various applications. The V/Hz mode is ideal for standard induction motor control, offering simplicity and efficiency. Sensorless Vector mode provides enhanced torque control without feedback devices, suitable for high-performance applications. Additional modes include Flux Observer and Closed-Loop Vector for precise speed and torque regulation. Each mode requires specific parameter configurations, such as motor nameplate data and load characteristics. Proper mode selection ensures optimal performance, energy efficiency, and smooth operation. Refer to the user manual for detailed setup instructions and parameter adjustments to match your application needs; Correct configuration prevents operational issues.
Operation and Control of the PowerFlex 525
The PowerFlex 525 drive offers intuitive operation and control, enabling precise motor speed adjustment and seamless integration with industrial systems.
Users can start, stop, and adjust frequency via the keypad, PLC, or external devices, ensuring flexible and efficient motor management.
Advanced control modes and real-time monitoring enhance operational accuracy and responsiveness.
4.1 Starting and Stopping the Drive
Starting and stopping the PowerFlex 525 drive is a straightforward process that can be initiated through various methods, including keypad controls, PLC signals, or external devices.
For keypad operation, users can directly input commands to start or stop the drive. When integrated with a PLC, the drive can be controlled via digital inputs, ensuring synchronized system operation.
It is crucial to ensure all safety precautions are in place before initiating operation. Additionally, the drive must be properly configured to recognize the control source.
The drive also features a “direct run” capability, allowing it to operate independently of a PLC, though this requires specific parameter settings. Always refer to the manual for detailed startup procedures.
4.2 Adjusting Frequency and Speed Parameters
Adjusting the frequency and speed parameters on the PowerFlex 525 drive can be done through various methods, ensuring precise motor control.
Using the keypad, users can directly input frequency values or adjust speed parameters in real-time. For external control, analog input signals or digital commands from a PLC can be utilized.
The drive supports multiple control modes, including Variable Frequency Control, allowing for energy-efficient operation. Parameter settings can also be configured via software tools for advanced customization.
Always refer to the manual for specific parameter details to achieve optimal performance and ensure safe operation.
4.3 Using the Keypad for Direct Control
The PowerFlex 525 drive allows for direct control using its integrated keypad, enabling easy parameter adjustments and operational commands.
Users can navigate through menus to set frequency, monitor motor status, and execute start/stop commands directly.
The keypad provides real-time feedback, simplifying troubleshooting and parameter customization.
For advanced control, the drive supports external devices, ensuring flexibility in industrial automation applications. Always refer to the manual for detailed keypad functionality.
Troubleshooting Common Issues
The PowerFlex 525 drive often encounters issues like fault codes, motor overload, and communication errors.
Identifying and resolving these problems ensures smooth operation and minimizes downtime.
5.1 Identifying and Interpreting Fault Codes
Fault codes on the PowerFlex 525 drive indicate specific issues, such as motor overload or communication errors.
For example, F007 signals an internal electronic overload, requiring load reduction.
Referencing the user manual or online forums provides detailed explanations and solutions.
Understanding these codes ensures rapid troubleshooting and minimizes downtime.
5.2 Resolving Communication Errors
Communication errors with the PowerFlex 525 often arise from incorrect IP settings or wiring issues.
Ensure the drive’s Ethernet port is properly connected to the network, and verify Modbus TCP/IP configurations match the PLC or HMI.
Consult the user manual for parameter settings and use diagnostic tools to test connections.
If issues persist, reset the drive or check for firmware updates.
For complex problems, refer to online forums or Rockwell Automation support for detailed troubleshooting guides.
5.3 Addressing Motor Overload and Overheat Issues
Motor overload and overheat issues on the PowerFlex 525 can be resolved by reducing the load or addressing excessive heat buildup.
Check for fault codes like F007 (motor overload) and ensure the motor is properly sized for the application.
Verify ambient temperature and ventilation to prevent overheating.
Inspect motor parameters in the drive settings and adjust as needed.
Regular maintenance, such as cleaning heat sinks, can prevent overheat conditions.
Consult the user manual for detailed troubleshooting steps and parameter adjustments to restore optimal operation.
Integration with PLC and SCADA Systems
The PowerFlex 525 seamlessly integrates with PLCs like Allen-Bradley and Siemens via Modbus TCP/IP, enabling remote monitoring and control through SCADA systems for enhanced industrial automation.
6.1 Connecting the Drive to a PLC (e.g., Siemens, Allen-Bradley)
To connect the PowerFlex 525 drive to a PLC, ensure proper wiring and communication setup. Use Modbus TCP/IP for Ethernet-based connections, configuring IP addresses and ports. For Siemens PLCs, verify compatibility and settings. Allen-Bradley PLCs integrate seamlessly via EtherNet/IP. Ensure the drive’s communication parameters match the PLC’s configuration. Test the connection post-configuration to confirm data exchange. Address potential issues like incorrect IP settings or module mismatches. Refer to the user manual for detailed wiring diagrams and parameter settings. Proper integration enables efficient control and monitoring of the drive from the PLC system.
6.2 Configuring Modbus TCP/IP Communication
To configure Modbus TCP/IP communication for the PowerFlex 525 drive, start by assigning an IP address and subnet mask to the drive. Ensure the PLC or master device is on the same network. Set the Modbus ID and TCP port number in the drive’s parameters. Use the user manual to locate the specific parameters for Modbus configuration. Verify that the PLC is programmed to communicate with the drive using the same settings. Test the connection to confirm data exchange. Proper configuration enables seamless communication and control between the drive and the PLC system.
6.3 Monitoring and Controlling the Drive Remotely
Remote monitoring and control of the PowerFlex 525 drive enable real-time supervision and adjustment of its operation. Using Allen-Bradley software or SCADA systems, users can access drive parameters, monitor performance, and receive alerts. Modbus TCP/IP communication is essential for transmitting data between the drive and the control system. This setup allows for precise control of speed, torque, and other operational aspects from a centralized location. Remote capabilities enhance maintenance by enabling predictive analysis and reducing on-site visits, thereby improving overall system efficiency and reliability. Proper network security measures must be implemented to safeguard remote access.
Maintenance and Upkeep of the PowerFlex 525
Regular maintenance ensures optimal performance and longevity of the PowerFlex 525. Inspect and replace wearable parts, update firmware, and adhere to safety standards for reliable operation.
7.1 Scheduled Maintenance Procedures
Scheduled maintenance for the PowerFlex 525 ensures reliability and longevity. Regularly inspect and clean the drive, check for firmware updates, and verify parameter settings. Lubricate moving parts, ensure proper ventilation, and maintain backup configurations. Adhere to safety standards outlined in the manual to prevent downtime and ensure optimal performance.
7.2 Replacing Wearable Parts and Components
Regularly inspect wearable parts like fans, capacitors, and connectors for signs of wear. Replace them as needed to prevent unexpected failures. Always use genuine Allen-Bradley parts for compatibility and performance. Before performing any replacement, disconnect power and follow safety guidelines in the manual. Ensure proper grounding and use anti-static precautions to avoid damage. Replace components in accordance with the manual’s instructions, and test the drive afterward to confirm functionality. Keep a record of replacements for future reference and compliance with maintenance schedules.
7.3 Ensuring Compliance with Safety Standards
To ensure compliance with safety standards, always follow the guidelines outlined in the PowerFlex 525 manual. Adhere to international and local regulations, such as those related to electrical and industrial safety. Use only genuine Allen-Bradley parts to maintain safety and performance. Properly install and maintain the drive according to the manual’s instructions. Conduct regular inspections and ensure all safety protocols are followed during operation and maintenance. Always disconnect power before servicing and use proper grounding techniques. Train personnel on safety procedures to prevent accidents and ensure compliance with industry standards. This ensures safe operation and longevity of the drive.
Advanced Features and Capabilities
The PowerFlex 525 offers advanced features like variable frequency control, remote monitoring, and customizable parameters for tailored applications, enhancing efficiency and performance in industrial automation systems.
8.1 Using Variable Frequency Control for Energy Efficiency
The PowerFlex 525 drive utilizes variable frequency control to optimize energy efficiency by adjusting motor speed according to load demands, reducing unnecessary energy consumption. This feature is particularly beneficial in applications where motors do not need to operate at full speed continuously. By varying the frequency and voltage supplied to the motor, the drive minimizes power usage while maintaining performance. This not only reduces operational costs but also lessens mechanical stress on the motor, extending its lifespan. Additionally, variable frequency control contributes to a quieter operation and reduced harmonic distortion, making it an eco-friendly and efficient solution for industrial automation systems.
8.2 Implementing Remote Monitoring and Control
The PowerFlex 525 drive supports remote monitoring and control through various communication protocols, enabling real-time supervision and adjustments. By integrating with PLCs or SCADA systems, users can access drive parameters, monitor performance, and receive fault notifications from a central location. Ethernet connectivity and Modbus TCP/IP compatibility simplify remote operations, allowing seamless integration into industrial networks. This feature enhances operational efficiency, reduces downtime, and enables predictive maintenance by providing insights into drive and motor performance. Remote control capabilities also allow for precise adjustments, ensuring optimal system operation without physical intervention, making it ideal for large-scale industrial automation setups.
8.3 Customizing Drive Parameters for Specific Applications
The PowerFlex 525 allows customization of drive parameters to suit specific industrial applications, ensuring optimal performance. By adjusting parameters like motor speed, torque, and acceleration, users can tailor the drive to their unique requirements. Advanced features enable precise control over voltage, frequency, and power, making it adaptable to diverse motor types. Customization can be achieved through software tools or direct parameter adjustments, ensuring compatibility with various industrial processes. Referencing the user manual is crucial to understand parameter functions and ensure correct configuration for specific tasks, maximizing efficiency and reliability in industrial automation systems. Regular testing of customized settings is recommended.
Resources and Support
The PowerFlex 525 drive is supported by comprehensive resources, including the official user manual, online forums, and technical support. Authorized distributors provide additional assistance and genuine parts.
9.1 Accessing the Official User Manual and Documentation
The official Allen-Bradley PowerFlex 525 user manual is available for download on Rockwell Automation’s website. This comprehensive guide provides detailed instructions for installation, programming, and troubleshooting. It includes technical specifications, parameter settings, and safety guidelines to ensure optimal drive performance. Users can access the manual in PDF format, making it easy to navigate and reference. For additional support, technical data publications like the PowerFlex 520-Series AC Drive Specifications (520-TD001) and user manuals (520-UM001) are also available. Always refer to official sources for accurate and up-to-date information.
9.2 Utilizing Online Forums and Technical Support
Online forums and technical support are invaluable resources for resolving issues with the Allen-Bradley PowerFlex 525 drive. Platforms like Rockwell Automation’s official forums and third-party communities provide solutions to common problems, such as configuration errors or fault codes. Users can share experiences, ask questions, and receive guidance from experts. Technical support teams are also available to address specific queries, ensuring timely troubleshooting and optimal drive performance. These resources empower users to resolve issues efficiently and maximize their understanding of the drive’s capabilities.
9.3 Finding Authorized Distributors and Service Providers
Locating authorized distributors and service providers for the Allen-Bradley PowerFlex 525 drive is essential for ensuring genuine parts and reliable support. Rockwell Automation’s official website provides a distributor locator tool to find certified partners worldwide. These providers offer authentic products, maintenance services, and technical assistance, ensuring compliance with factory standards. Verifying a distributor’s authorization is crucial to avoid counterfeit products and maintain warranty validity. By leveraging these official channels, users can access trusted resources for drive repair, replacement, and upgrades, ensuring optimal performance and longevity of their equipment.